APOLLO LP
- Filling machines with rotary pistons -
Linear filling machines with Lobe pumps dosing system (Apollo LP) are mainly intended for filling of dense products and products with pieces of fruits, vegetables, nuts etc. The machine can be used in food, pharma and cosmetics industry.
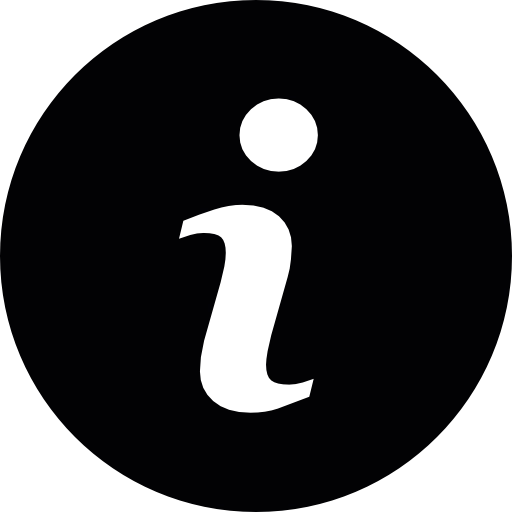
- Machine stainless frame mounted on height adjustable legs
- Motorized stainless steel conveyor with adjustable speed
- Infeed and outfeed gates which locates the group of bottles under the filling nozzles
- Bottle presence sensor
- Lobe pumps for dosing of the product
- Rise while fill nozzles
- Closing of the filling nozzles (anti-drip system)
- Anti-collission control of filling nozzles
- Bottle neck support for neck alignment
- Anti-drip tray under the filling nozzles
- Control of bottles evacuation
- Sensor to detect full downstream conveyor
- Siemens controller with touch screen
- CE safety guards
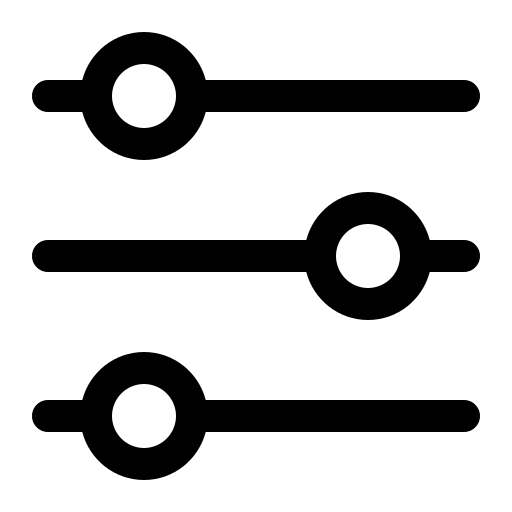
- Product tank made of AISI 304 or AISI 316 with level control
- Pressurized product tank CIP inlet connection
- Spray ball inside product tank
- Set of adapters for nozzles cleaning
- Weight cells under the filling nozzles
- Motorized lift of filling nozzle
- Remote access
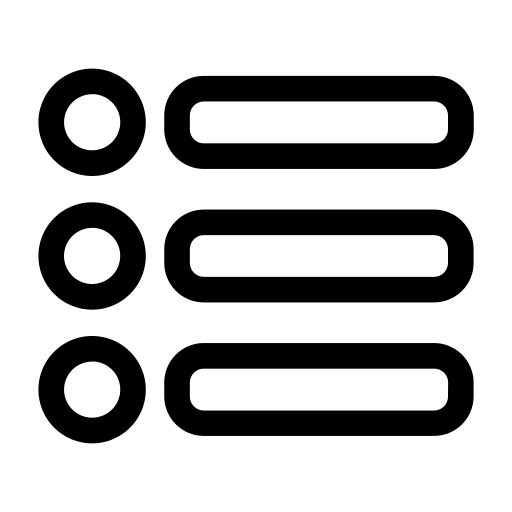
- The containers enter the machine on the conveyor with plastic or stainless steel belt. Before entering the filling area, they are stopped by inlet pneumatic gate. Once the previous group of filled containers leaves the filling station, the gate opens and allows next group of containers to enter. The inlet gate is closed again afterwards. In case one or more containers are missing, the system waits and the filling process does not start.
- After entering of all the bottles, the filling process starts. As soon as the bottle necks are automatically centered, the nozzles dive into the bottles and open. The dose is measured and dosed by Lobe pumps. The filled dose is adjustable from the touch screen, which enables fast and easy change of the dosing volume and parameters.
- After finishing of the filling process, the nozzles close and the drip tray comes under the nozzles to avoid staining the containers. Then the outlet gate opens and lets the containers out of the filling machine.
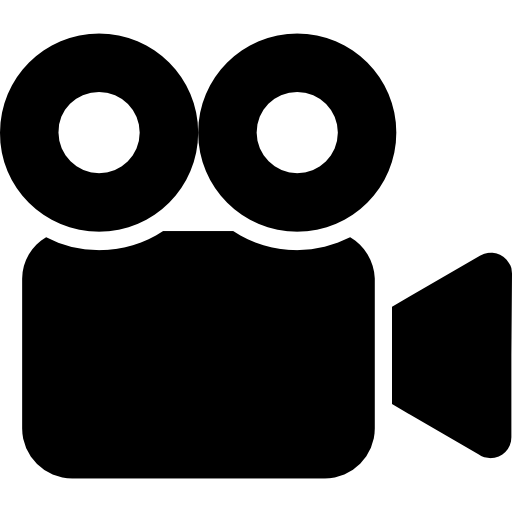