Capline Dynamic: The Future of Capping Machines
Increasing Efficiency and Productivity with Capline Dynamic
In today's manufacturing environment, efficiency and precision are paramount. Businesses are constantly seeking innovative solutions to streamline their production processes and reduce costs while ensuring product quality. One such groundbreaking solution is the Capline Dynamic, a fully automatic continuous capping machine that revolutionizes the capping process.
This article aims to shed light on the remarkable features and benefits of the Capline Dynamic, showcasing its ability to optimize operations and elevate productivity.
Unleashing the Power of Capline Dynamic:
The Capline Dynamic sets itself apart by combining cutting-edge technology with a user-centric design. Its linear configuration eliminates the need for format parts, enabling seamless adaptation to different container sizes.
Let's delve into the machine's exceptional features that make it a game-changer in the industry:
Stainless Steel Construction: The robust machine frame, crafted from high-quality stainless steel, ensures durability and longevity. Adjustable legs provide flexibility for optimal setup and ergonomics in any production environment.
Motorized Conveyor with Adjustable Speed: The motorized stainless steel conveyor offers adjustable speed capabilities, allowing precise control over the container's movement through the capping process. This ensures synchronization and minimizes the risk of product splashing.
Stabilization and Guidance: Adjustable side belts within the Capline Dynamic stabilize and guide the bottles during capping, further enhancing accuracy and consistency.
Caps Orientator: Equipped with a rotary caps orientator, the Capline Dynamic ensures that caps are properly aligned before capping. This meticulous process guarantees efficient closure application and reduces potential bottlenecks.
Cap Chute and Sensor: The integrated cap chute, coupled with a sensor for cap presence check, ensures that only correctly oriented caps are used. This safeguards against any potential disruptions or malfunctions.
Pick and Place Device: Capline Dynamic employs a pick and place device, leveraging dynamic servodriven technology to accurately grasp and position caps onto containers. This cutting-edge mechanism adapts to the container's movement, tightening caps with the requested torque during transport.
Sensor Technology: With a bottle presence sensor and an encoder system controlling bottle and canister speed, the Capline Dynamic maintains a smooth and efficient workflow. It optimizes production by detecting full downstream conveyors and seamlessly adjusting to varying production rates.
User-Friendly Control Panel: The Capline Dynamic features a control panel with a touch screen interface, simplifying machine operation and providing real-time monitoring of critical parameters. Operators can effortlessly manage settings and track performance, ensuring seamless integration into existing production lines.
Safety Guards and Options: The Capline Dynamic is designed with safety as a top priority. Equipped with safety guards, it prioritizes the well-being of operators. Additionally, optional features like ATEX execution, chemical proof execution, remote access, and a rejector for bottles without caps cater to specific industry requirements.
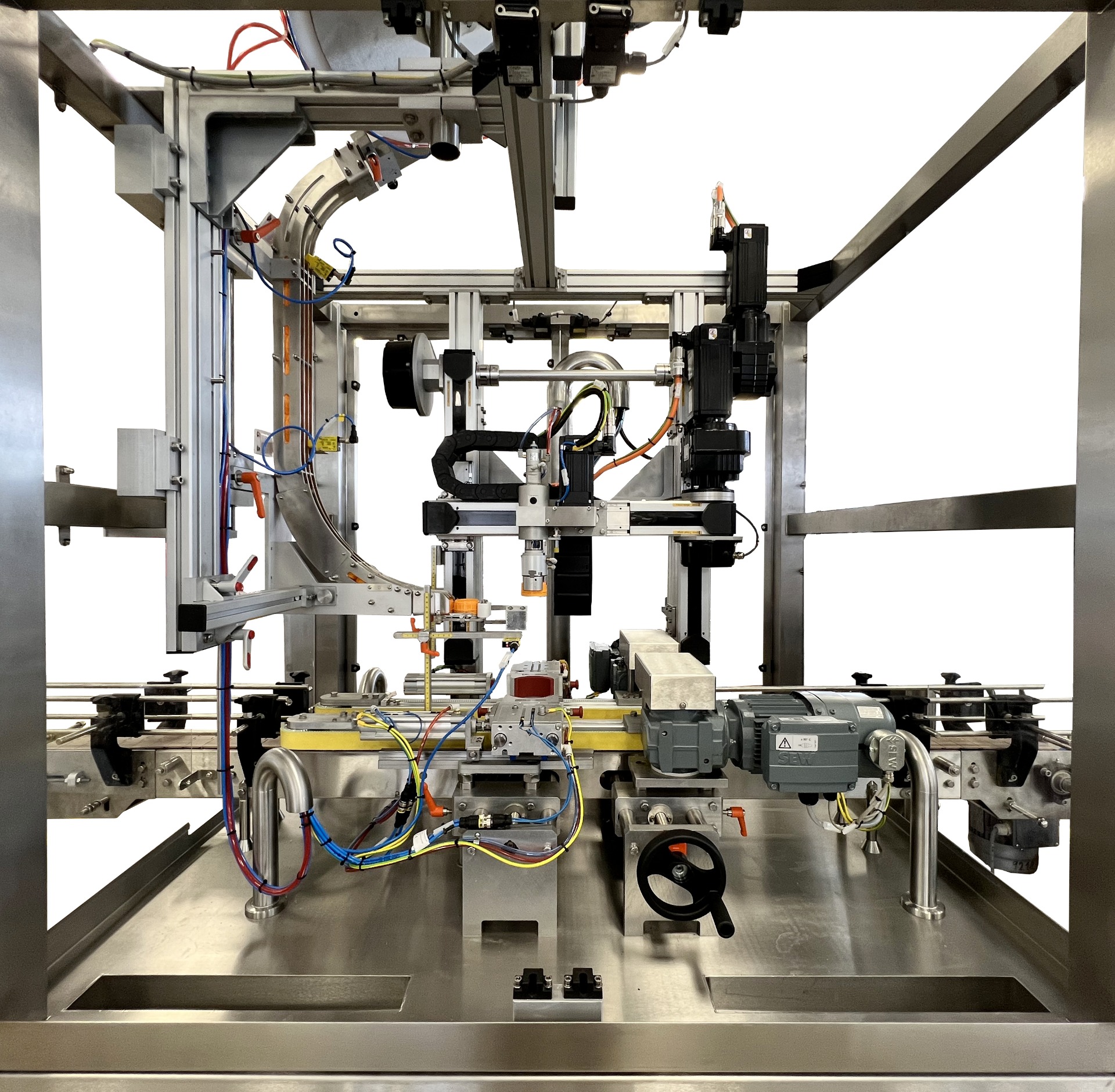
Process Description:
The operational excellence of the Capline Dynamic is exemplified by its streamlined capping process. As the container enters the machine on the conveyor belt, it is stabilized and guided by adjustable side belts. The caps, meticulously oriented through a vertical or rotary caps orientator, seamlessly transition through the cap chute to the pickup point. Dynamic servodriven capping heads then secure the caps onto the moving containers, ensuring precise torque application. Finally, closed bottles gracefully exit the machine on the downstream conveyor, ready for the next phase of production.